车架作为摩托车关键零部件,其精度直接影响装配性,操控性。周进在宝马项目时,便一直在全力提升车架精度,并让技术走在了行业前列。进入无极(VOGE)后,他并未邀功自满,而是继续对车架精度提升试验,让无极产品的品质,站在前沿。
选对方法,提高精度的第一步
在传统工艺下,团队在切割和焊接程序上无论如何严控,焊接成品总会产生形变,精度符合率不到30%,工艺提升迫在眉睫。
从工艺源头梳理问题,发现要从切割件精准程度提升入手,让原材料符合标准。
团队经过多次试验后,发现激光切割法能将切割管件合格率提高到约97%,焊接后成品车架精度符合率也提升至约65%。虽进步巨大,但仍未达到宝马标准。
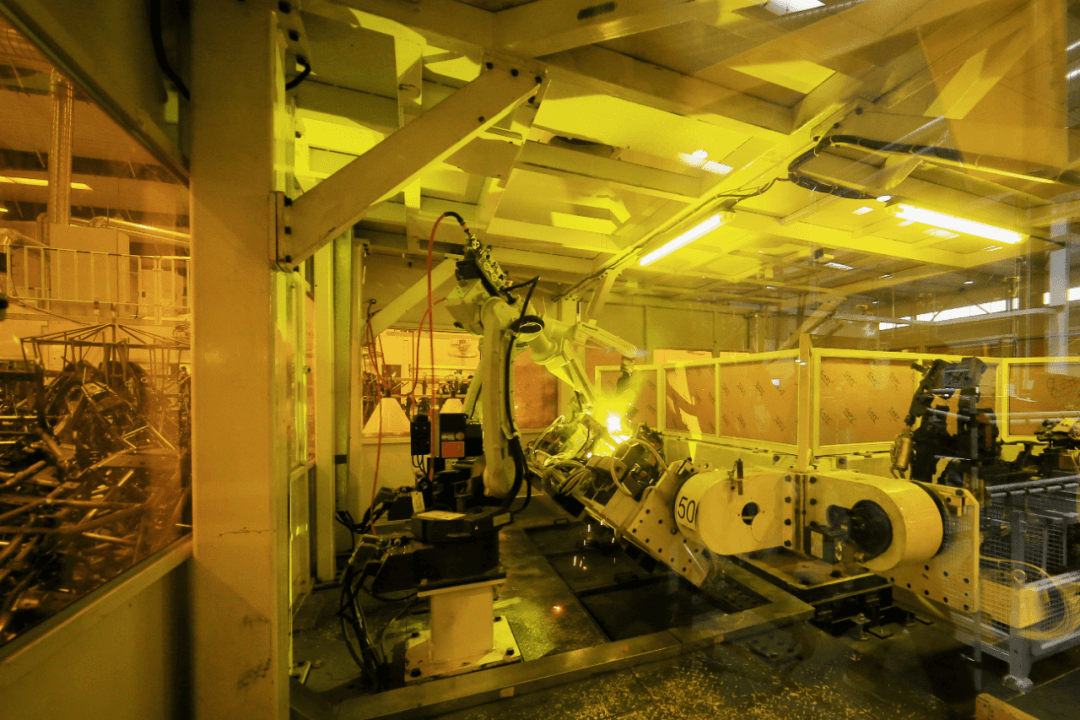
协调矛与盾,击破精度挑战
为了能顺利达标,团队重新检测分析优化车架,确定车架焊接与结构刚性这两个问题互有影响,就像矛与盾,只考虑单一方向,很难真正解决问题,必须整体考虑。
周进说:“为这两个问题,我们经常因为结果不对,推翻以前所有过程,重新再来,不断调整,交叉试验,让问题影响逐渐降低。”
不论是对焊接点做周密的测算,调试焊接机器人程序和运行轨迹;还是对车架结构重新扫描,计算最佳受力角度,不断假设各种受力情况,确保车架在受力时能够保持刚性、不会轻易变形。团队坚持双线同步进行,往往一次试验耗费数日甚至数周,繁琐枯燥成为常态。
一环一环的优化整个焊接工艺,让车架精度符合率达到了近80%,逼近了宝马标准。
在近一年、上千次试验、报废上百个车架、采集几千个数据后,车架精度符合率达到近99%,不仅满足了宝马标准,更直接走在了行业前列。
贯彻标准,坚持向前一步
周进说:“当初团队几乎都经历过好多次睡办公室、在厂房铺纸板打地铺的日子,我们一直在想办法跟时间赛跑,坚持把事情做好。只有好的结果,才说明我们的付出有价值。”
如今在无极车架的打造上,沿用并优化以往工艺,取得了更大的技术突破,对细节的不懈打磨,让产品驾驶体验更加极致。